Why Thermography?Therma-Scan
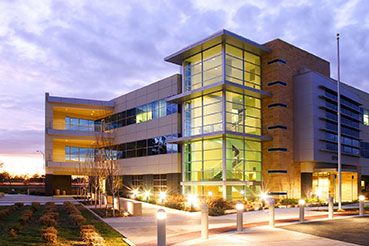
In these days of 24/7 continuous operation, performing a non-evasive test under normal operation will help eliminate potential problems and help maintain the uptime level of the facility.
By having an active thermographic program as part of the predicative maintenance program, the findings can help save companies money by helping to eliminate unplanned equipment outages and costly repair costs, not to mention business disruptions.
Managers and maintenance staff should understand the importance of performing thermographic surveys and evaluate their current thermographic program to see if it requires any part of it to be updated.
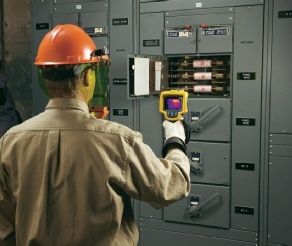
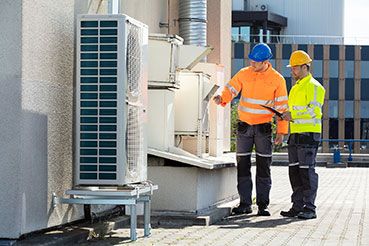
Not all equipment needs to be included in a thermographic survey. Companies need to continually evaluate what equipment is included in their thermographic survey and to update the thermographic program for new equipment that has been added to the facility since the last survey was taken. Older equipment may not be as critical and used less so that it may no longer be required to be scanned and should be removed from the program. A thermographic survey needs to be continually updated and reviewed to ensure that it is providing the best data possible.
Frequently Asked Questions
- What is a thermographic survey?
- Can anyone use a thermographic camera?
- What are some common items that can affect a scan?
- What are predictive maintenance programs and why are they used?
- What are the cost benefits to having a thermographic survey?
- What equipment needs a thermographic scan?
- How often is a thermographic survey needed?
What is a thermographic survey?
Can anyone use a thermographic camera?
A thermographer who does scanning on structural buildings is not necessarily going to be able to perform an electrical scan. The thermographer must understand what the readings are telling them and how to perform that type of scan to get the most accurate readings. Some types of thermographic scans can require very specialized equipment to be able to perform the specified tasks, and only a small number of people invest the resources and time in training on the specialized equipment.
What are some common items that can affect a scan?
In the case of electrical equipment, the equipment must be online carrying load. The load level is important because if the equipment is lightly loaded, the equipment may not show a hot spot even if there is a poor connection point. Because of the load issue, the thermographer has to take amp readings to determine if the equipment will be able to show a connection problem.
Air currents can affect the surface readings of equipment. The air current can cool the surface of the equipment but not provide enough cooling to the internals of the equipment. This can lead to a missed problem if the equipment is not isolated from potential air currents during thermographic scans. If the air currents cannot be isolated, the thermal readings must be compensated for by adjusting for air temperature and air speed to arrive at an accurate temperature reading.
What are predictive maintenance programs and why are they used?
Depending on the type of equipment being analyzed, the equipment may require different types of testing. Thermographic surveys can improve the predictive nature of maintenance programs by showing where the equipment is generating hot or even cold spots that are not normal in the operation of the equipment. A thermographic survey using a non-evasive testing routine allows the equipment to remain online in an operational mode. Once a potential problem has been identified, further testing by other means may be required to pinpoint the cause of the failure. With the data from the thermographic survey, during a scheduled maintenance window the maintenance staff can then perform other types of testing that may require the equipment to be taken offline and test equipment connected. This allows the maintenance staff to make better informed decisions and to ensure that potential problems are addressed in a timely manner.
What are the cost benefits to having a thermographic survey?
What equipment needs a thermographic scan?
Equipment that has recently been started up
Equipment that has recently been started up should always have a thermographic scan performed. This will provide two pieces of information. The first piece of information is that the equipment was installed properly and is working correctly. The second piece of information is what will be used over the life of the equipment, and that is a thermographic baseline of the equipment. In future thermographic surveys, the baseline will be used to determine how much deviation has accrued and to point out excessive deviation that needs to be corrected.
Equipment that is going to be shut down for an extended period of time
Performing a scan on equipment that is going to shut down allows the maintenance staff to verify that everything is operating properly before the shut down and requires no follow up testing. If a problem is identified, the maintenance staff can schedule repair during the shut down period and avoid having the equipment offline for repairs when the equipment is scheduled to be online.
Additional types of equipment that may need a thermographic survey
- Equipment that is never removed from service for maintenance due to the critical nature of the equipment. This is very important for checking cable connections and bus bars in electrical equipment and switchboards and to verify that all connections are tight and there is no corrosion causing a poor connection.
- Equipment that is exposed to vibration or mechanical movement. By conducting the thermographic survey, it can reveal both electrical and mechanical heating caused by loose connection, misalignments and worn out bushings.
- UPS batteries can have a thermographic scan performed during a battery run down. The thermographic scan will help identify batteries with poor connections on the battery posts. A thermographic scan may also reveal hot spots or cold spots inside the battery showing that the battery is not performing as it should.
- Power distribution units should have thermographic scans performed on them yearly. These units carry a lot of different loads and usually are never taken offline for maintenance. Not only can loose connections on the panel board breakers show up, but also the thermographic scan can show that the breaks are reaching a point where they are going to fail by showing hot spots internally in the breakers. The scan will also be able to inspect the transformer for any problems.
How often is a thermographic survey needed?
FAQs
By just using a thermographic camera, a person cannot necessarily produce an accurate report. Not all material is equal when performing a scan on it. The reason is that different materials will emit thermal energy differently. Depending on the type of material, a darker object may be better than a shiny object for taking readings on. Shiny objects, glass and plexiglass will reflect thermal readings from other sources and will not give an accurate reading. This is the reason that the person performing the scan needs to be experienced and properly trained on how to conduct a scan and to interpret the thermal readings.
A thermographer who does scanning on structural buildings is not necessarily going to be able to perform an electrical scan. The thermographer must understand what the readings are telling them and how to perform that type of scan to get the most accurate readings. Some types of thermographic scans can require very specialized equipment to be able to perform the specified tasks and only a small number of people invest the resources and time in training on the specialized equipment.
All equipment covers need to be removed so that an accurate scan can be performed. Even if you can see through the safety covers, the plexiglass safety covers will not allow a reading to be taken through them and will only reflect other sources of thermal energy back towards the camera. During the performance of the thermographic survey, reflections from thermal sources must be considered and eliminated as a potential source of the infrared reading.
In the case of electrical equipment, the equipment must be online carrying load. The load level is important because if the equipment is lightly loaded then the equipment may not show a hot spot even if there is a poor connection point. Because of the load issue, the thermographer has to take amp readings to determine if the equipment will be able to show a connection problem.
Air currents can affect the surface readings of equipment. The air current can cool the surface of the equipment but not provide enough cooling to the internals of the equipment. This can lead to a missed problem if the equipment is not isolated from potential air currents during thermographic scans. If the air currents cannot be isolated then the thermal readings must be compensated for by adjusting for air temperature and air speed, to arrive at an accurate temperature reading.
Companies use predictive maintenance programs to identify potential failure of components before the components have actually failed. The program allows the maintenance staff to repair components during a scheduled repair window by knowing that a piece of equipment is approaching its failure point. This allows the maintenance staff to be proactive instead of being in a reactive mode of fixing equipment only when it fails. By using this method, the maintenance staff can have on hand the proper tools and replacement parts needed to repair a piece of equipment without the equipment having to be out of service for extended periods of time.
Depending on the type of equipment being analyzed, the equipment may require different types of testing. Thermographic surveys can improve the predictive nature of maintenance programs by showing where the equipment is generating hot or even cold spots that are not normal in the operation of the equipment. A Thermographic survey using a non-evasive testing routine allows the equipment to remain online in an operational mode. Once a potential problem has been identified, further testing by other means may be required to pinpoint the cause of the failure. With the data from the thermographic survey, during a scheduled maintenance window, the maintenance staff can then perform other types of testing that may require the equipment to be taken offline and test equipment connected. This allows the maintenance staff to make better informed decisions and to ensure that potential problems are addressed in a timely manner.
The cost of having a thermographic survey performed can easily be outweighed by the potential failures that can be identified and corrected. A good thermographic survey can identify problems that could lead to overloaded equipment tripping offline or causing a fire. Motors and pumps can have potential bearing problems or shaft alignment problems identified before a motor burns up and must be totally replaced instead of a minor repair performed on the motor. In most cases, when a single problem is identified, the potential loss if that equipment was to fail would easily cost more than the thermographic scan plus the remedial maintenance.
This can be a very hard question to answer. The two pieces of equipment that can readily be identified are equipment that has recently been started up and equipment that is going to be shut down for an extended period of time.
Equipment that has recently been started up
Equipment that has recently been started up should always have a thermographic scan performed on them. This will provide two pieces of information. The first piece of information is that the equipment was installed properly and is working correctly. The second piece of information is what will be used over the life of the equipment and that is a thermographic base line of the equipment. In future thermographic surveys, the base line will be used to determine how much deviation has accrued and to point out excessive deviation that needs to be corrected.
Equipment that is going to be shut down for an extended period of time
By performing a scan on equipment that is going to shut down, it allows the maintenance staff to verify that everything is operating properly before the shut down and requires no follow up testing. If a problem is identified, then the maintenance staff can schedule repair during the shut down period and avoid having the equipment offline for repairs when the equipment is scheduled to be online.
Additional types of equipment that may need a thermographic survey
- Equipment that is never removed from service for maintenance due to the critical nature of the equipment. This is very important for checking cable connections and bus bars in electrical equipment and switchboards and to verify that all connections are tight and there is no corrosion causing a poor connection.
- Equipment that is exposed to vibration or mechanical movement. By conducting the thermographic survey, it can reveal both electrical and mechanical heating caused by loose connection, misalignments and worn out bushings.
- UPS batteries can have a thermographic scan performed during a battery run down. The thermographic scan will help identify batteries with poor connections on the battery posts. A thermographic scan may also reveal hot spots or cold spots inside the battery showing that the battery is not performing as it should.
- Power distribution units should have thermographic scans performed on them yearly. These units carry a lot of different loads and usually are never taken offline for maintenance. Not only can loose connections on the panel board breakers show up but the thermographic scan can show that the breaks are reaching a point where they are going to fail by showing hot spots internally in the breakers. The scan will also be able to inspect the transformer for any problems.
Types of Equipment to be Scanned
Switchboards
Panel boards
Panel boxes
Switch disconnects
Fuse disconnects
Fuse holders
Transformers (air and oil)
PDUs
Bus duct
Cable terminations
Power cabling
Neutral cablings
Batteries
Control panels
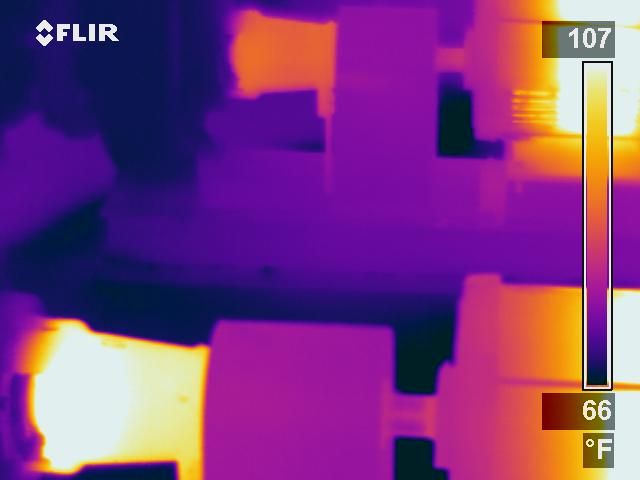
Pumps
Motors
Shaft couplings
Air duct blockage
Oil cooling channels
Vent cooling
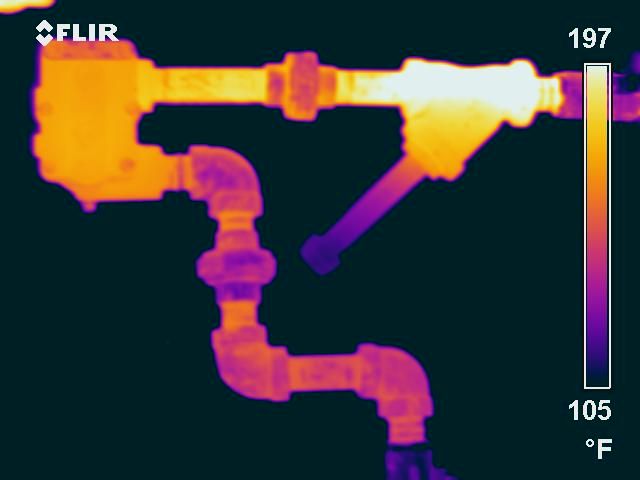
Water pipes
Cooling pipes
Steam pipes
Material buildup in a vacuum
Piping
Roof leakage
Wall insulation
Floor insulation
Ceiling Insulation
Concert wall construction
Weather seals